by Amy Jeary
Surgical robotics has already revolutionized many surgical applications and will continue to do so, allowing for minimally invasive procedures that result in faster recovery times, less pain, and fewer complications for patients. However, the success of robotic surgeries depend on the precision and accuracy of the console’s individual components, and this is where precision machining and manufacturing come in.
Precision machining and manufacturing involve the use of advanced computer-controlled machines to produce highly accurate and consistent components. In surgical robotics, these critical components include the end-effectors and patient interfacing instruments, camera and visualization instruments, the surgeon’s control module, and robotic arms for translating motion.
To achieve the precision required in surgical robotics, manufacturers use a variety of techniques, such as computer-aided design (CAD), computer-aided manufacturing (CAM), and computer numerical control (CNC) machining. These techniques enable manufacturers to produce surgical robotic system components that meet tight tolerances, ensuring a perfect fit and maximum efficiency.
In addition to precision, the materials used in surgical robotics must also be biocompatible and durable. This means that the components must not cause any adverse reactions in the patient’s body, and they must be able to withstand repeated use and sterilization.

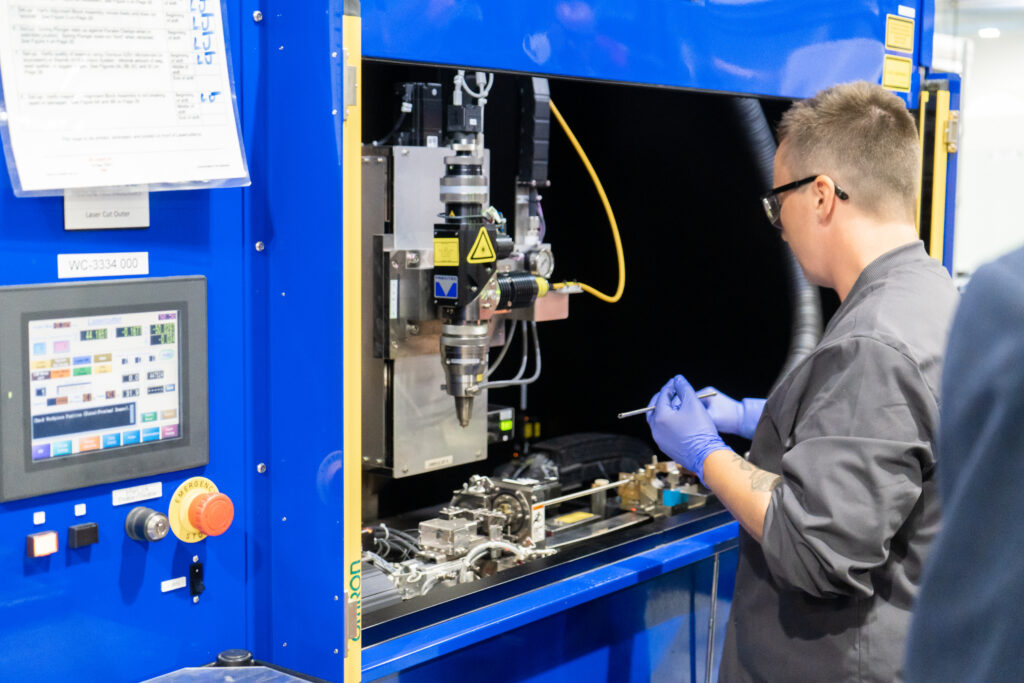
To achieve these requirements, manufacturers use a variety of materials, including titanium and stainless steel, which are known for their biocompatibility and strength. These materials can be machined to very high tolerances using CNC machines, ensuring a perfect fit and maximum durability.
Precision machining and manufacturing also play a critical role in the maintenance and repair of surgical robotic equipment. In the event of a malfunction or breakdown, precision machined replacement parts can be quickly and easily installed, ensuring that the system is up and running as quickly as possible.
Precision machining and manufacturing are essential in the development of surgical robotics. The precision and accuracy of the components used in surgical robots are critical to their success, and the use of advanced manufacturing techniques ensures that these components meet the requirements of modern surgical applications. By using advanced materials, precise machining techniques, and rigorous quality control measures, manufacturers can produce high-quality components and tools that meet the demanding requirements of surgical robotics.

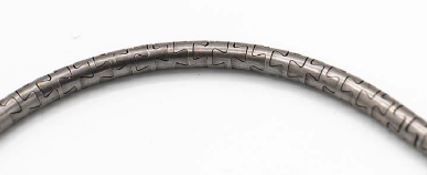
Nissha Medical Technologies (NMT) has been the trusted end-to-end solutions partner in design, development, and manufacturing for global MedTech OEMs for over 30 years. NMT’s recent acquisition of a medical machining facility has added assembly, over-molding of machined components to their vertically integrated list of capabilities. Although new to NMT, the acquired facility in Norwalk, OH has been offering full-service machining to medical OEMs for over 60 years, with an emphasis in lens polishing, lens grinding, and complex lens train assembly.